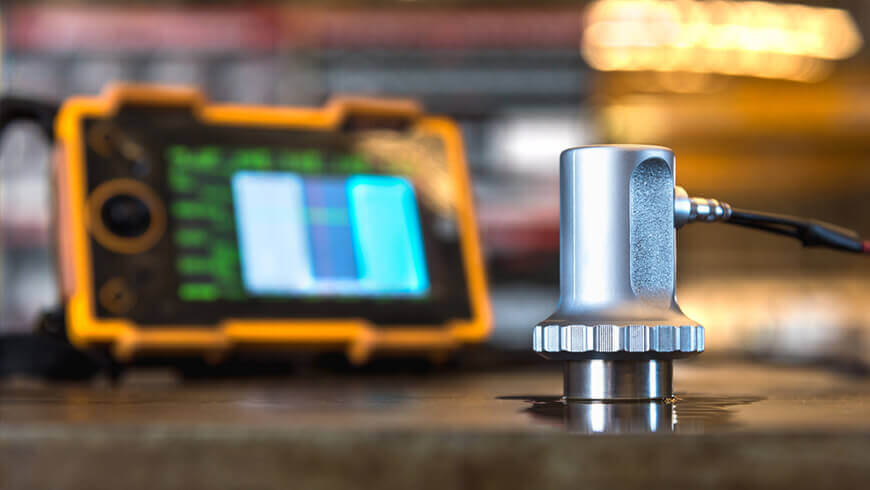
Ultrasonic Testing
Ultrasonic testing (UT) is a family of non-destructive testing techniques based on the propagation of ultrasonic waves in the object or material tested. In most common UT applications, very short ultrasonic pulse-waves with center frequencies ranging from 0.1-15 MHz, and occasionally up to 50 MHz, are transmitted into materials to detect internal flaws or to characterize materials. A common example is ultrasonic thickness measurement, which tests the thickness of the test object, for example, to monitor pipework corrosion.
Ultrasonic testing is often performed on steel and other metals and alloys, though it can also be used on concrete, wood and composites, albeit with less resolution. It is used in many industries including steel and aluminium construction, metallurgy, manufacturing, aerospace, automotive and other transportation sectors.
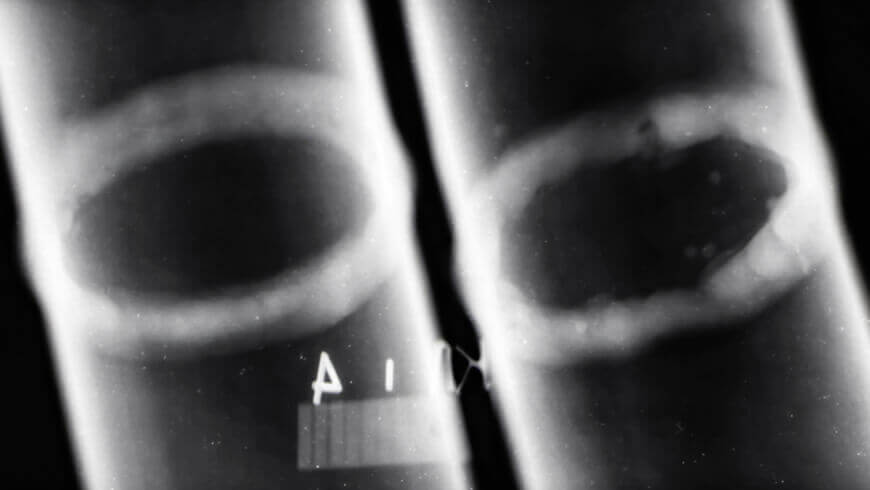
Digital Radiography
Digital radiography is a form of radiography that uses x-ray–sensitive plates to directly capture data during the examination, immediately transferring it to a computer system without the use of an intermediate cassette. Advantages include time efficiency through bypassing chemical processing and the ability to digitally transfer and enhance images. Also, less radiation can be used to produce an image of similar contrast to conventional radiography.
Instead of X-ray film, digital radiography uses a digital image capture device. This gives advantages of immediate image preview and availability; elimination of costly film processing steps; a wider dynamic range, which makes it more forgiving for over- and under-exposure; as well as the ability to apply special image processing techniques that enhance overall display quality of the image.
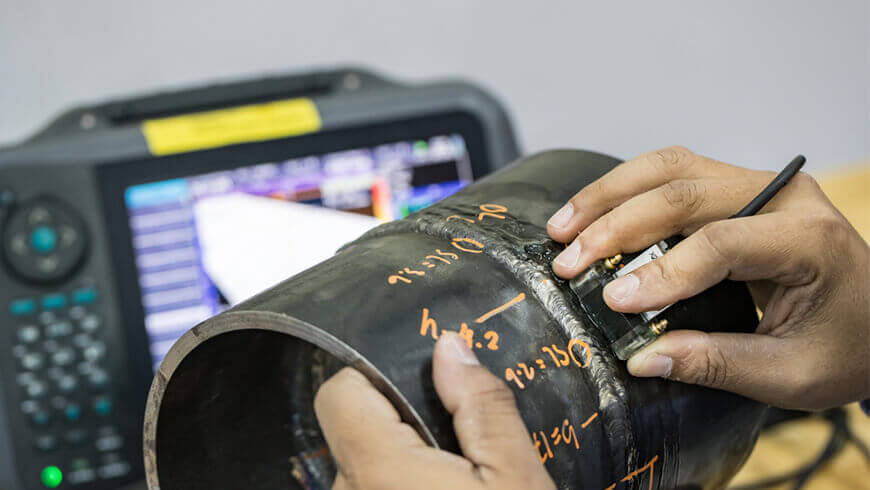
Phased Array
Phased array ultrasonics (PA) is an advanced method of ultrasonic testing that has applications in medical imaging and industrial nondestructive testing. Common applications are to noninvasively examine the heart or to find flaws in manufactured materials such as welds. Single-element (non-phased array) probes, known technically as monolithic probes, emit a beam in a fixed direction. To test or interrogate a large volume of material, a conventional probe must be physically scanned (moved or turned) to sweep the beam through the area of interest. In contrast, the beam from a phased array probe can be focused and swept electronically without moving the probe. The beam is controllable because a phased array probe is made up of multiple small elements, each of which can be pulsed individually at a computer-calculated timing. Phased array ultrasonic testing is based on principles of wave physics, which also have applications in fields such as optics and electromagnetic antennae.
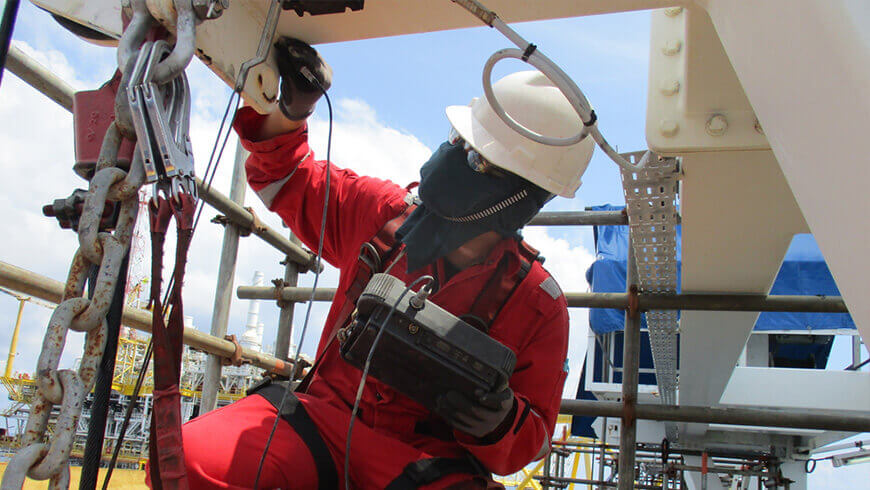
Eddy Current
Eddy current testing (ECT) as a technique for testing finds its roots in electromagnetism. When there is a closed path through which current can circulate and a time-varying magnetic field passes through a conductor (or vice versa), an electric current flows through this conductor. Eddy current testing is now a widely used and well understood inspection technique for flaw detection, as well as thickness and conductivity measurements.
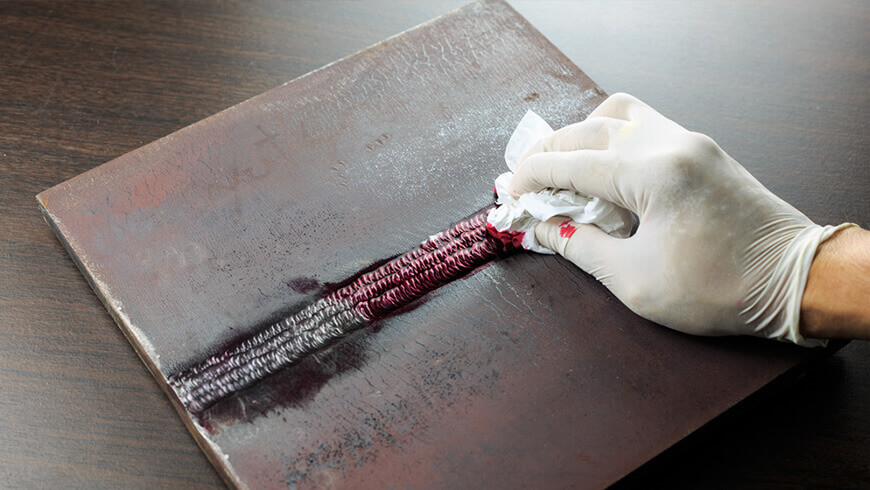
Dye Penetrant
Dye penetrant inspection (DPI), also called liquid penetrant inspection (LPI) or penetrant testing (PT), is a widely applied and low-cost inspection method used to check surface-breaking defects in all non-porous materials (metals, plastics, or ceramics). The penetrant may be applied to all non-ferrous materials and ferrous materials, although for ferrous components magnetic-particle inspection is often used instead for its subsurface detection capability. LPI is used to detect casting, forging and welding surface defects such as hairline cracks, surface porosity, leaks in new products, and fatigue cracks on in-service components.
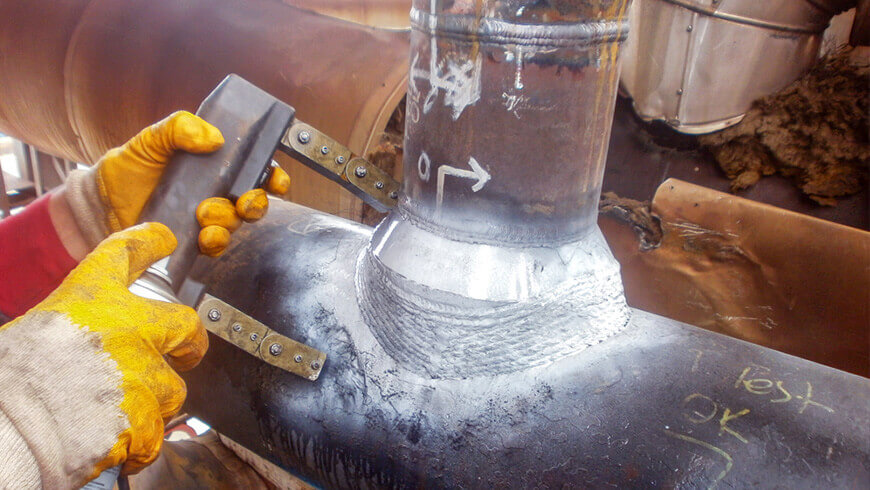
Magnetic Particle Inspection
Magnetic particle inspection (MPI) is a non-destructive testing (NDT) process for detecting surface and shallow subsurface discontinuities in ferromagnetic materials such as iron, nickel, cobalt, and some of their alloys. The process puts a magnetic field into the part. The piece can be magnetized by direct or indirect magnetization. Direct magnetization occurs when the electric current is passed through the test object and a magnetic field is formed in the material. Indirect magnetization occurs when no electric current is passed through the test object, but a magnetic field is applied from an outside source. The magnetic lines of force are perpendicular to the direction of the electric current, which may be either alternating current (AC) or some form of direct current (DC) (rectified AC).
The presence of a surface or subsurface discontinuity in the material allows the magnetic flux to leak, since air cannot support as much magnetic field per unit volume as metals.
To identify a leak, ferrous particles, either dry or in a wet suspension, are applied to a part. These are attracted to an area of flux leakage and form what is known as an indication, which is evaluated to determine its nature, cause, and course of action, if any.
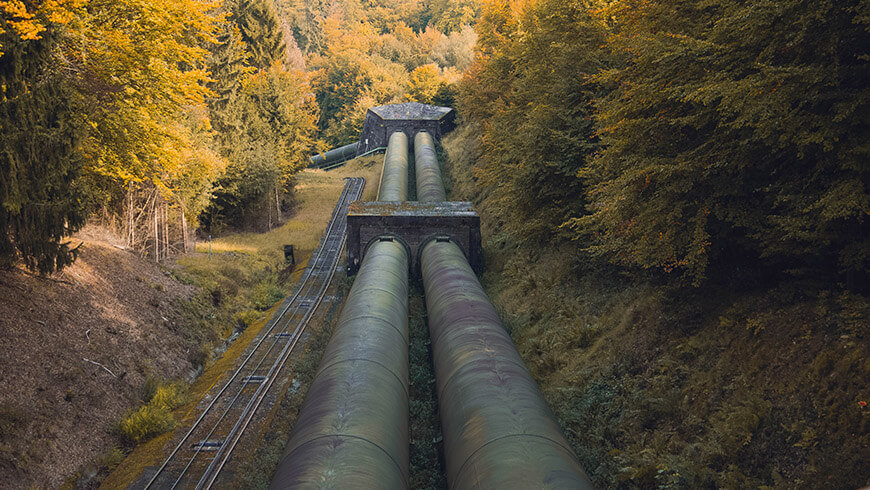
Visual Inspection
Visual inspection is a common method of quality control, data acquisition, and data analysis. Visual Inspection, used in maintenance of facilities, mean inspection of equipment and structures using either or all of raw human senses such as vision, hearing, touch and smell and/or any non-specialized inspection equipment. Inspections requiring Ultrasonic, X-Ray equipment, Infra-red, etc. are not typically regarded as Visual Inspection as these Inspection methodologies require specialized equipment, training and certification.
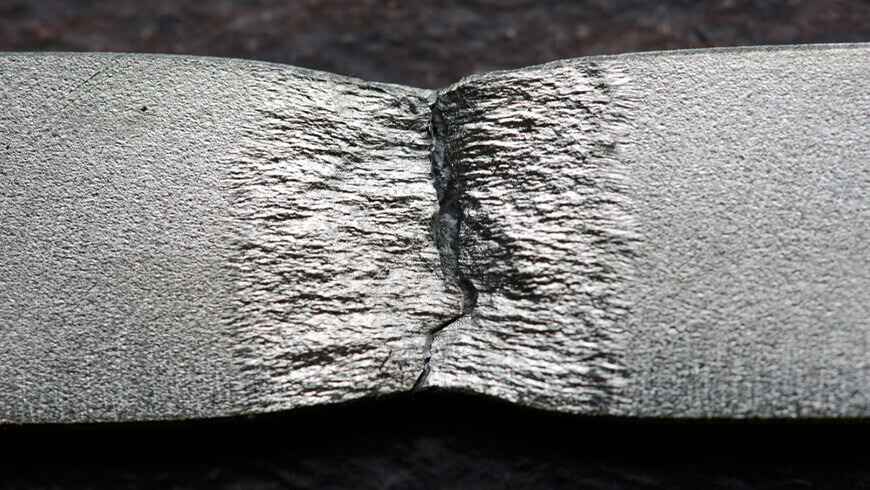
Tensile Testing
Tensile testing, also known as tention testing is a fundamental materials science and engineering test in which a sample is subjected to a controlled tension until failure. Properties that are directly measured via a tensile test are ultimate tensile strength, breaking strength, maximum elongation and reduction in area.
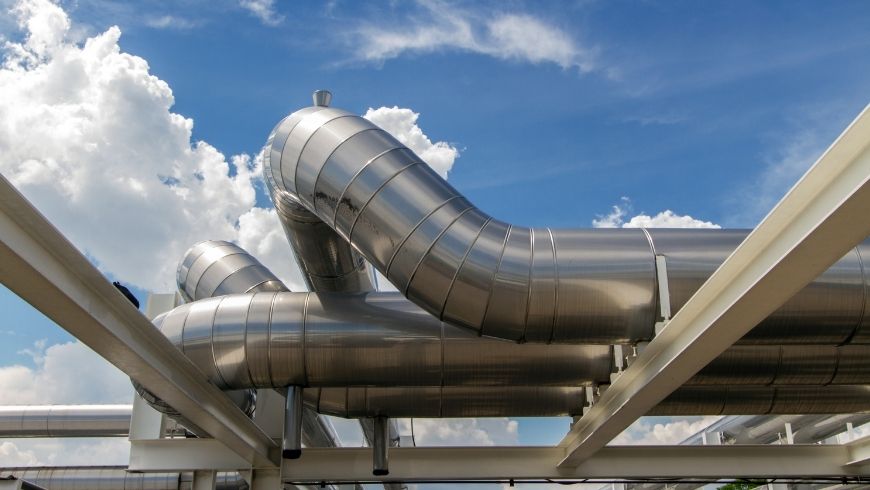
Ammonia Refrigeration System Inspection
ITI's services for ammonia refrigeration systems offer cost-effective and efficient testing without compromising the integrity of your insulated pipe by using:
Digital Radiography (DR)
- Real-time Radiography (RTR) – CUI Scanner
- Moisture Detection Imaging (MDI)
- Infrared Thermography (TNDT)
ITI offers detailed Computer-Generated Reports that:
- Displays every DR image including wall thickness
- Real-time video or picture of areas of interest
- Percentage of wall loss
- Isometric drawings of piping and associated equipment